Diag FMEA, the software to help you to set up predictive maintenance : Assist in choosing the right monitoring solution, depending on the failure mode observed.
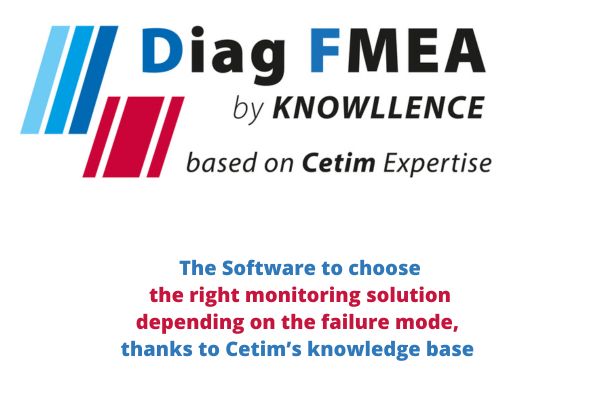

A successful partnership: Diag FMEA is the result of the combination of Cetim’s expertise and Knowllence’s ability to digitize risk management.
The Diag FMEA software allows manufacturers to find monitoring solutions to optimize the predictive maintenance of their equipment and products.
Diag FMEA is intended to be used ;
- To help engineers optimize the maintenance of their future equipment
- To help maintenance department to replace parts at the right time, rather than blindly and systematically
- To make maintenance companies more profitable with fixed-price maintenance
It can be used to optimize maintenance management, production facilities, public works machinery, lifting equipment, etc.
This is a full web solution (SaaS available).
How to Reduce Maintenance Costs the Right Way?
By diagnosing early warning signs and failures, the maintenance department can analyze the most critical faults and prioritize its actions by selecting the most appropriate solutions from the knowledge base. This enables the maintenance department to take part in an iterative process of improving predictive maintenance and sharing solutions.
How can machine monitoring be integrated right into the design process?
The designer carries out a functional analysis and looks for the main functions of its future equipment. He thinks about potential failures and draws on the knowledge base to choose the right sensors, continuous or periodic monitoring.
These concerns: machines, production equipment, machinery (public works, lifting equipment, etc).
Transversal a knowledge base, based on Cetim’s expertise
CETIM’s knowledge base includes around 250 detailed fact sheets on sensors and instrumentation, in French and English. You can enrich this database your own data.
The objective is to structure and share feedback.
Predictive maintenance: better than conventional FMEA studies
The Design FMEA and the Process FMEA identify potential failures in a product or manufacturing process during the design phase and initiate an action plan to reduce their causes.
The Machinery FMEA, identifies failures and their causes (as well as effects) on people’s safety and on the unavailability of machine functions. Makes it possible to launch action plans to eliminate the most critical ones right from (the machine) design stage.
In these 3 cases of “classic” FMEA, it is often impossible to resolve the failure because it is too expensive, so we put the machine under permanent surveillance (costly) and replaced systematically and at planned intervals (costly).
Because Diag FMEA takes a different point of view at an earlier stage in the process, it can identify failures and determine the most critical ones, both in the design and maintenance phases. Diag FMEA helps you to make decisions on these critical points by proposing solutions in Cetim’s knowledge base.
This makes it possible to set up less pricy maintenance and helps to reduce the company’s environmental impact, since analysis of the data collected enables parts to be changed only when necessary!
What Diag FMEA offers?
- Guide you through the functional analysis and the failure analysis table from a “maintenance” point of view
- Identify and evaluate actual or potential failures
- To make the diagnosis and choosing the right monitoring;
- either in design, by integrating diagnostic elements as early as possible
- or on a tablet, as close as possible to the machine to find sensor ideas
- Facilitate collaboration and manage action plans
- Structure, standardize diagnostics, analyses and share data
- A Risk Analysis Assessment is automatically generated for design and maintenance reviews
- Enrich your company’s knowledge base with your feedback, race and cross-reference the choices made, save time on following studies
- Facilitate the implementation of ISO 17359:2018 “Condition monitoring and diagnostics of machines” to which Cetim contributed within the framework of the standardization process.
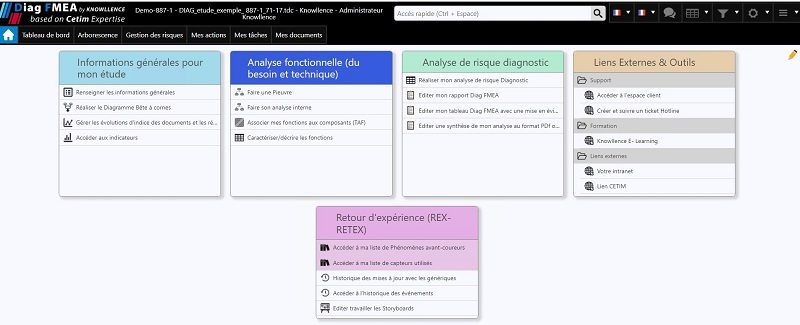
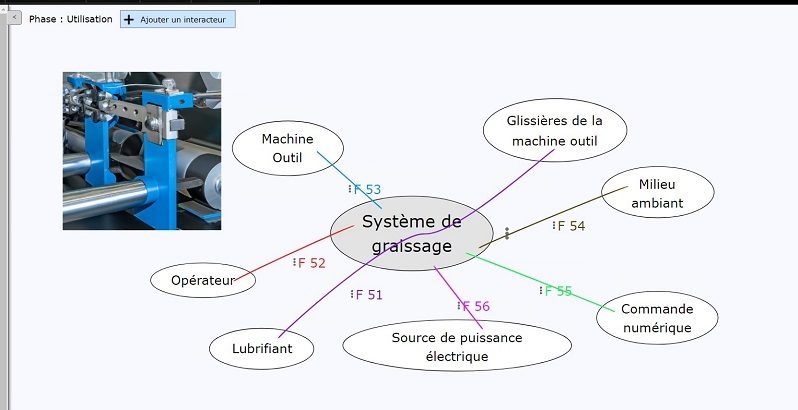
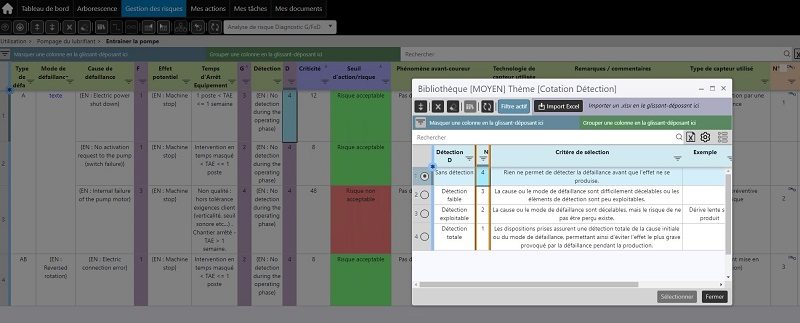