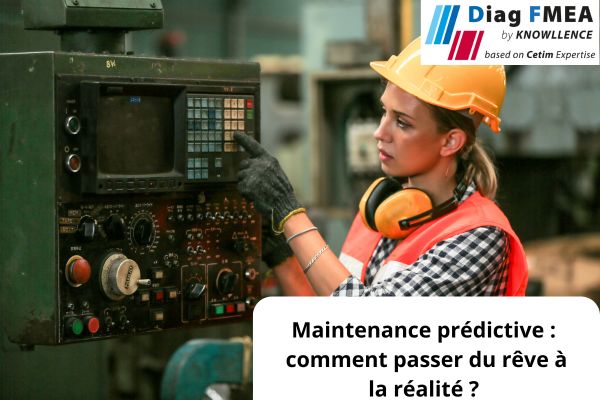
Un marché révolutionnaire
Depuis quelques années, les solutions de maintenance prédictive qui permettent d’anticiper les défaillances grâce à l’utilisation de capteurs connectés et des logiciels d’analyses et d’anticipation grâce à l’intelligence artificielle ou l’apprentissage automatique sont florissantes.
La maintenance prédictive aspire à détecter les pannes potentielles et les défaillances avant qu’elles ne se produisent. Cela permet aux entreprises d’éviter tout arrêt coûteux de la chaîne de production et donc de réduire les coûts non planifiés.
Les chiffres que l’on peut trouver sur les sites et brochures sont alléchants : réduction des coûts de maintenance de 10 à 40%, réduction du nombre de pannes de moitié, montant d’investissement diminué de 5%, etc. Il est certain que la mise en place de la maintenance prédictive au sein d’une entreprise est une solution indéniable pour optimiser les coûts de maintenance. Mais n’y-a-t-il pas quelques facteurs à prendre en compte avant de s’y lancer à bras ouverts ?
Quels équipements cibler ?
Suffit-il de mettre l’intégralité de nos machines sous surveillance, avec un capteur de vibration ou de température, laisser notre nouveau logiciel analyser les données et nous prévenir lorsqu’une donnée semble anormale ? Pas si simple.
L’une des premières étapes dans la mise en place de notre maintenance prédictive ou conditionnelle est le choix des machines que l’on veut mettre sous surveillance. Plusieurs facteurs peuvent entrer en compte. Il faut d’abord comprendre quelles machines au sein du process de production sont dites critiques. Ce sont des équipements dont les défaillances peuvent avoir des conséquences graves sur le personnel, l’environnement, le respect de la réglementation et l’arrêt de la production.
Si pour une panne d’un équipement, les pièces de remplacement sont à bas coûts, ou peuvent être changées rapidement,… et que l’impact de la panne sur le process est minime, rester sur une stratégie de maintenance curative reste une solution pertinente et plus économique.
Analyse des modes de defaillance
Pour mettre sous surveillance votre machine, il faut d’abord la connaître. Connaître ses fonctions, ses interacteurs, ses composantes mécaniques et électroniques. Ces informations sont généralement connues par les réparateurs, utilisateurs et concepteurs de ces machines, mais ne sont pas souvent répertoriées. Conduire une analyse fonctionnelle sur vos machines critiques peut permettre de délimiter vos périmètres d’action et de prioriser encore un peu plus vos analyses de défaillances sur les fonctions les plus critiques de votre équipement.
Une analyse des modes de défaillances de type AMDEC peut être conduite afin de mettre en évidence les défaillances les plus critiques sur votre équipement. Sur ces défaillances critiques, il faut maintenant trouver les propriétés qui annoncent la défaillance imminente : les signes avant-coureurs (température anormale, vibrations, contamination du fluide, etc.).
Quels types de capteurs ?
Une fois que vous avez priorisé vos machines, les défaillances critiques, puis établit les propriétés physiques à surveiller, vous pourrez choisir les bonnes solutions de surveillance (capteurs).
Oui, le rêve est devenu réalité. Cette méthode analytique en amont est capitale pour conduire à bien votre migration vers une maintenance prédictive. Comment la mener à bien ?
DIAG FMEA : GUIDE POUR VOTRE MAINTENANCE PREDICTIVE
Le Cetim, spécialisé dans l’étude des défaillances mécaniques, a mis en place en collaboration avec Knowllence, spécialiste en analyse des risques, la solution web Diag FMEA.
Diag FMEA est un logiciel qui permet de suivre la méthodologie expliquée ci-dessus de manière rigoureuse. La base de données issue de l’expertise du Cetim aide également à trouver les signes avant-coureurs des défaillances potentielles des équipements, et propose automatiquement des solutions de surveillances pertinentes à mettre en place sur votre équipement.
MAINTENANCE PREDICTIVE
Une fois les différentes solutions choisies, l’anticipation des pannes est rendue possible par :
– l’implantation de ces capteurs. Ils permettront de remonter les données.
– la modélisation d’un schéma de panne. En se basant sur l’historique de fonctionnement des machines.
– le développement et l’optimisation d’algorithmes prédictifs qui déterminent les seuils d’alerte.
CONCLUSION
La maintenance prédictive offre un potentiel considérable pour améliorer l’efficacité et la fiabilité des opérations de maintenance.
Cependant, il est crucial de reconnaître et de comprendre les limites inhérentes à cette approche. Une analyse préalable approfondie des machines, des capteurs appropriés, de la fiabilité des données, de la complexité des machines et des coûts associés est essentielle pour une mise en œuvre réussie de la maintenance prédictive. En reconnaissant ces limites, les entreprises peuvent utiliser cette technologie en l’intégrant dans une stratégie plus globale de maintenance pour optimiser la performance de leurs machines et de leurs équipements.